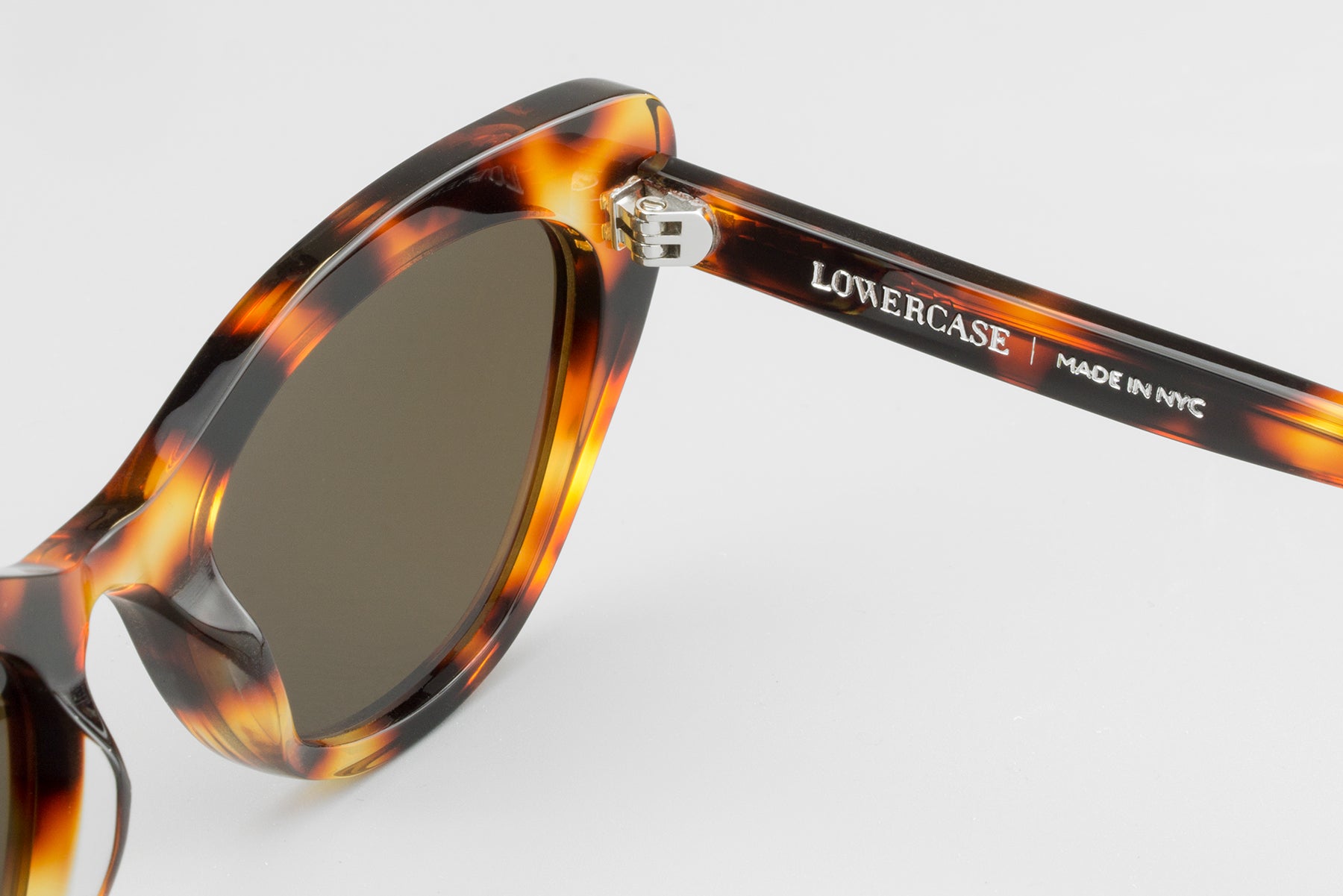
Not just another pair of sunglasses
We founded Lowercase in 2016 with a mission: to once again localize the trade of eyewear to the US, while creating a product that is unparalleled in quality and design.
We are part of an emerging movement in American manufacturing: we operate at a small scale and prioritize craftsmanship above all else. We design, build and finish each and every frame in our Brooklyn Army Terminal workshop, and proudly label our frames Made in NYC.
Our unique, small-batch manufacturing process combines new technology with traditional handcrafting techniques: The value of our approach can be seen in our designs and felt in the construction.
Anatomy of a Lowercase Frame
Craftsmanship always comes first, resulting in a product that stands apart from the rest. Every Lowercase frame goes through a meticulous construction process, consisting of thirty steps and requiring two weeks to complete.
The Designs
Our designs are inspired by New York: the architecture, people, and culture that make up the city. Manufacturing in house allows for a creative and flexible design process. Adding and removing even a millimeter of acetate can change the whole look of a frame: every design goes through several rounds of testing and editing before being put into production.
Read more about our design process and how we choose acetates for our frames.
Hardware is sourced from OBE, a German company supplying the eyewear industry with the highest quality precision hardware for over a century. Our acetate comes from Italy and Japan, and we are proud to outfit our sunglasses with Carl Zeiss lenses.
How it's Made
Lowercase at the Brooklyn Army Terminal from Lowercase NYC on Vimeo.
Finishing
Every pair of frames goes through an extensive ten-step finishing process.
Barrel tumbling, hand filing and various forms of hand polishing are employed to give the acetate its signature shine.
Read more about our finishing technique.
Once the frames are finished, we cut their lenses and do a final fit and quality check.